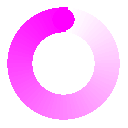
Preview of Mark Graban's AME Australia "Road Show" in 2025 - #Lean Continuous Improvement
Learn more and register: www.ame.org.au/events-training/upcoming-events/roa…
Hi! G'day! I'm happy to be partnering with AME Australia on a "Road Show" to conduct workshops in various cities in March and April 2025.
Ready to create a workplace culture that thrives?
A winning workplace culture requires a foundation of Psychological Safety and Problem Solving. Join Mark Graban, renowned expert in Lean and continuous improvement, for two engaging and hands-on half-day workshops designed to help you drive better results and build a stronger culture of continuous improvement in your organisation.
Both workshops are interactive, engaging, and packed with practical takeaways for leaders and teams across any industry or company size. Don’t miss the chance to learn from Mark Graban and transform the way you improve!
Session 1 - Psychological Safety as a Foundation for Continuous Improvement
Session 2 - Measures of Success: React Less, Lead Better, Improve More
Session One
Psychological Safety as a Foundation for Continuous Improvement
Psychological Safety is the foundation for any effective Lean Management System or continuous improvement effort—at Toyota, or any organisation. It can be described as an individual's feeling or perception that they feel safe, in a given situation, to speak candidly, without punishment, about topics including:
Problems
Questions
Mistakes
Ideas
Psychological Safety means feeling safe disagreeing with your manager (or a colleague) and hashing out the best ideas on their merits. It means feeling safe asking questions, saying "I don't know," and challenging the status quo. It's not a bunch of feel-good mumbo-jumbo; Psychological Safety drives better business results.
What Attendees Will Learn
What Psychological Safety is (and is not)
The "4 stages of Psychological Safety" and how teams progress
Key leader behaviors that cultivate a sense of Psychological Safety
Connections to continuous improvement practices and why people need to feel safe to share ideas and safe to experiment with possible improvements
Session Two
Measures of Success: React Less, Lead Better, Improve More
Do you feel like you're chasing your tail – reacting to every up and down in your performance data? Do you get frustrated with being asked to come up with explanations for every “below average” data point or any day that doesn't hit the target? Are people in your organization wasting time chasing metrics instead of working to systematically improve the system?
If so, I have an interactive workshop for you! We’ll play the “Red Bead Game,” as made famous by the late Dr. W. Edwards Deming. We’ll have fun and learn practical methods and lessons.
What Attendees Will Learn
Create and interpret “Process Behavior Charts”
Distinguish between “signal” and “noise” in performance metrics
Evaluate projects and improvement efforts to look for statistically-meaningful and sustained improvement
Understand the pitfalls of methods including “red/green” analysis and linear trendlines
Connect these methods to your Lean Management System
Who Should Attend
This workshop series is ideal for leaders, managers, and team members from any industry or company size who are eager to strengthen their workplace culture and continuous improvement efforts.
Whether you’re in manufacturing, healthcare, education, or service sectors, if you’re responsible for leading teams, overseeing processes, or driving improvement initiatives, these sessions offer valuable tools and insights. Attendees will gain practical strategies to build a culture of trust and psychological safety, enabling team members to speak up, share ideas, and drive improvements without fear.
The workshops also suit anyone involved in data analysis or metrics interpretation, especially if you’re frustrated by constant reactive responses to data changes. You’ll learn how to differentiate meaningful performance trends from random fluctuations, allowing for more effective decision-making and sustained improvement.
コメント